A sustainability focused redevelopment of a Sydney heritage listed building has been commended by judges at the 2014 Sustainability Awards.
Legion House by Francis-Jones Morehen Thorp (FJMT) was chosen from the Large Commercial category which was won by 8 Chifley Square by Lippmann Partnership in collaboration with Rogers Stirk Harbour and Partners.
The judges commended FJMT for choosing technologies and techniques that could become a yardstick for larger scale projects in the future.
“This small project is not a typical commercial space, but a boutique project established by the developer (Grocon) as a test bed for technologies and techniques that may be deployable at a larger scale in other projects,” the judges' statement reads.
“Legion House is a refurbishment of existing buildings, yet has been designated as an “Autonomous Zero Carbon Life Cycle Building” under Australian Sustainable Built Environment Council definitions and has a 6 star Green Star (Office Design V3) rating.
“The building responds to its less than optimum context (receiving little sun or wind) by deploying biomass gasification for energy production. Air conditioning is provided by chilled beams and the building is also water balanced.
“This is an exemplary project which utilises its small scale and significant financial investment to deploy a range of innovative systems and strategies to minimise energy use.
“On this basis the project deserves commendation and the jury looks forward to future projects that scale up these techniques into large commercial market-feasible projects.”
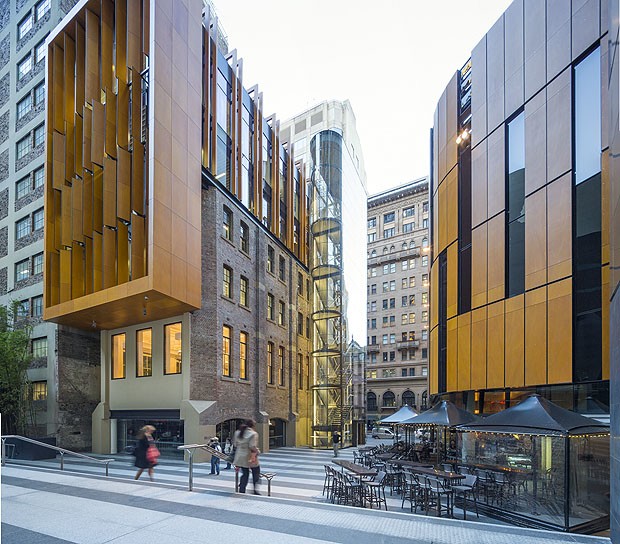
As part of its redevelopment, Legion House acquired an additional two levels (now five levels in total) along with state-of-the-art technology, making this building one of the most sustainable designs in the world.
Legion House receives its energy from a process called biomass gasification. The technology coverts plant sourced materials into a combustible gas that is used to generate electricity. This is effectively a carbon zero energy source as the greenhouse gases released in the energy production equal that absorbed in creating the biomass.
Legion House was certified by the Green Building Council of Australia with a 6 Star Green Star - Office v3 Design rating. Legion House is to be refurbished as a fully zero carbon building as it creates its own renewable electricity on site, resulting in zero net carbon emissions.
Key initiatives:
-
Legion House was refurbished as a Carbon Neutral building, and is technically classified as an ‘Autonomous Zero Carbon Life Cycle Building’ under the Australian Sustainable Built Environment Council definitions
-
The building is disconnected from the electricity grid and uses renewable energy to offset carbon emissions from its operations and embodied energy over the life cycle of the building
-
Receiving little sun or wind, Legion House receives its energy from a process called biomass gasification. The technology coverts plant sourced materials into a combustible gas that used to generate electricity. This is effectively a carbon zero energy source as the greenhouse gases released in the energy production equal that absorbed in creating the biomass
-
Legion House can utilise the commercial paper waste generated from the adjacent office tower through shredding and compressing this waste into the form of paper briquettes, which is then used in the gasification plant to produce usable Syngas
-
Air conditioning is provided throughout Legion House using chilled beam technology. The ventilation provided with the chilled beam system uses 100% fresh outside air to maintain a very high level of indoor environment quality for the occupants
-
Designed to be water balanced. This means that in a year of typical Sydney rainfall, all the amenity and operational water needs of the building will be met through rain captured on the roof. This is achieved through the use of advanced water conservation technology, high efficiency fixtures, vacuum toilets and the use of high quality rainwater recycling
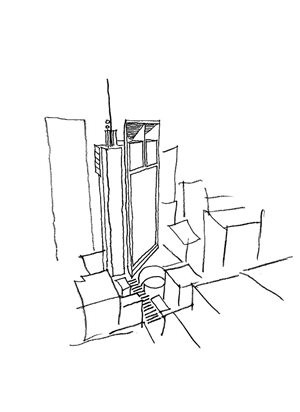

Images: John Gollings & Andrew Chung
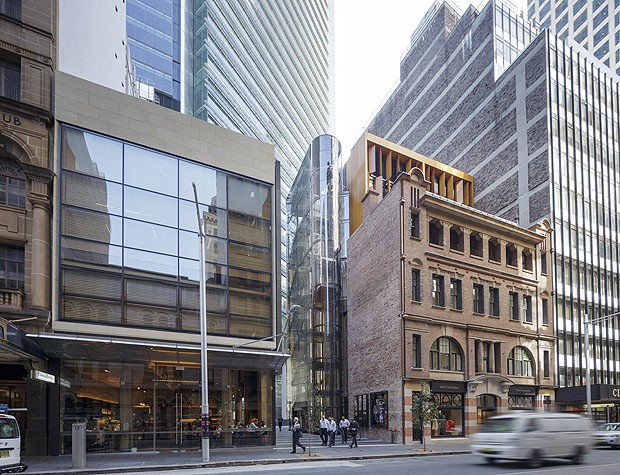
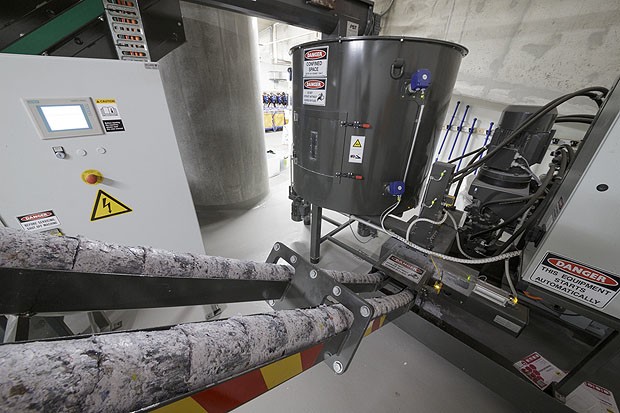
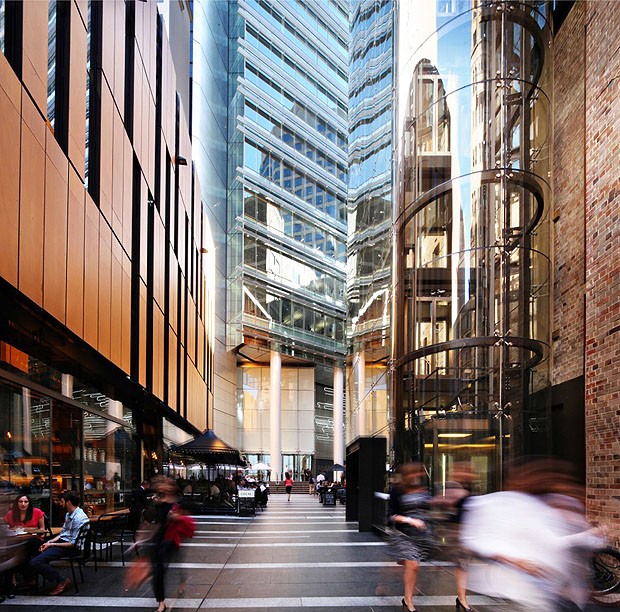



All the finalists can be viewed in the video below: