The challenges
Elanor Investors Group approached the redevelopment of the Belconnen Fresh Food Markets with a vision to offer Canberrans a European-style integrated fresh food market and casual dining precinct, all under one roof.
In creating the vision for Capital Food Market, the group teamed up with Stewart Architecture, project manager Lockbridge, and builder Construction Control to design an iconic building and premier food attraction to serve the Canberra community.
The Market’s design aimed to provide a light and open market space that is in keeping with the personal and interactive fresh food shopping experience. The building is naturally ventilated ensuring a minimal carbon footprint both in construction and operation well into the future. Thermal comfort is maintained through careful selection of building elements and appropriate heating and cooling strategies without air conditioning.
In a collaborative effort, the Capital Food Market design and construction team worked closely and proactively to find solution-driven outcomes. Site constraints and construction adjacent an operational market led to innovative solutions for materials and access.
Capital Food Market selected Bondor’s SolarSpan® all-in-one insulated panel, consisting of the roof, insulation and ceiling in a single panel, as a cost-effective and thermally superior alternative to traditional roofing.
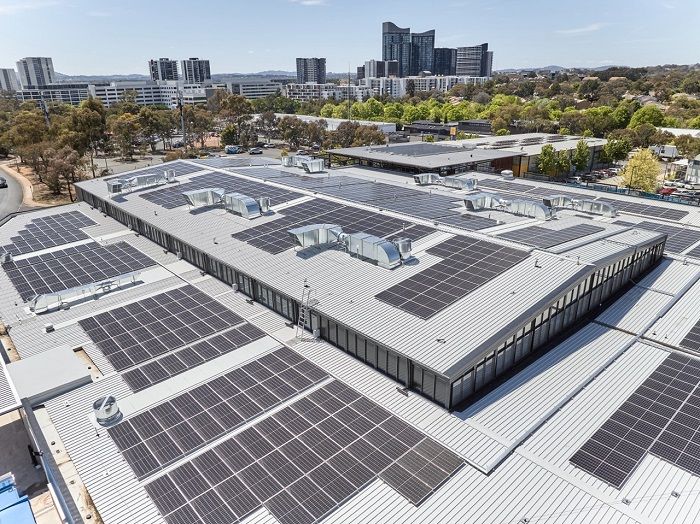
The solution
A key feature of Capital Food Market is the reimagining of the European market and dining experience, with both fresh food providores and restaurants all under the one roof.
During the specification process, Construction Control explored options to create a naturally ventilated space with a vaulted ceiling and long spans to foster the open market feel.
Construction Control Project Manager David Hodgson said Bondor’s SolarSpan offered a range of solutions to help meet the vision for Capital Food Market to meet performance outcomes in an economical and efficient way.
“SolarSpan’s extremely long spans meant we could cut down on the amount of structural steel required for the build, which provided a more open space within the market,” he said.
“The long spans available in SolarSpan allowed for full-length panels to be installed from ridge to gutter, which reduced the time for roof installation considerably.
“We were working on a restricted site, with an existing market on one side, roads on three other sides, and a basement carpark below. Due to the large footprint of the site we had to use mobile cranes and at times were restricted to lifting only a couple of days a week to minimise disruption to neighbouring business operations and the roads bordering the site.
“SolarSpan also significantly reduced installation time and cost by providing a complete system. Unlike traditional metal roof construction, the SolarSpan panels enabled large areas of finished ceiling, insulation, and roof to be installed in minutes and further finishing trades were not required.”
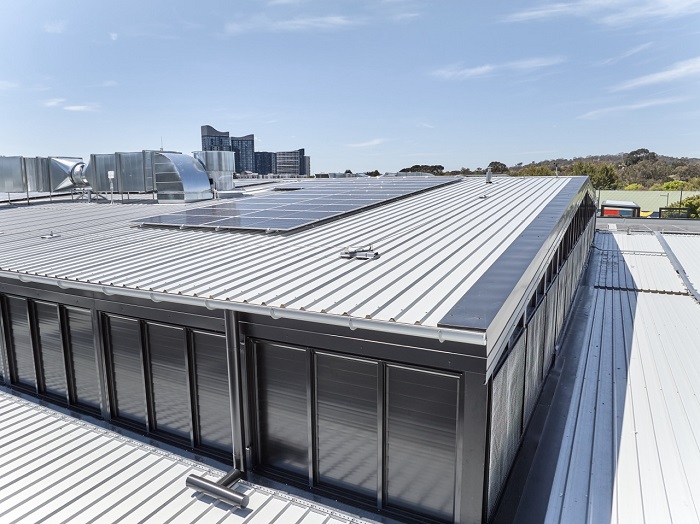
Hodgson said the 200mm panel thickness also allowed for continuous box gutters to reach the full depth of the panel, reducing the likelihood of gutter leaks at junctions.
A key criteria for roof selection also included a solar array to be installed on the roof to align with the owner’s environmental objectives. In conjunction with Bondor engineers, a large solar system was designed and installed without compromising the roof system.
“Another massive plus was that we could use a 50mm Bondor product that supported the box gutter and again provided a neat finish underneath without the need for additional finishes.”
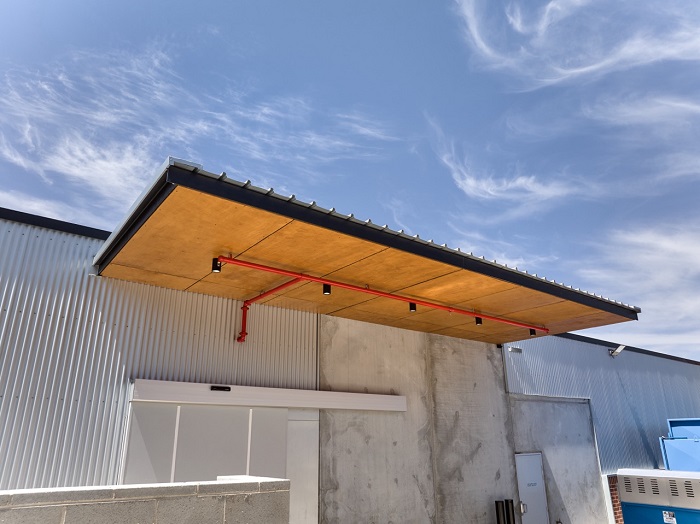
SolarSpan’s high thermal efficiency provided excellent thermal properties to meet the specific requirements of thermal comfort modelling. This allows Capital Food Market to achieve year-round optimal thermal comfort.