Background
With decorative turrets, tiled roofing and a vibrant blue and white colour scheme across three high-rise towers, the Bel Air Apartments are a Gold Coast icon. Instantly recognisable to locals and accommodating 263 apartments and 12 retail outlets, the resort-style buildings have become a treasured feature of the busy Broadbeach skyline.
Built in 2001, the Bel Air Apartments are in a highly corrosive C5 environment positioned directly opposite to the ocean and near the busy Gold Coast Highway and tramline.
Repainted in 2011, the building’s exterior facade was beginning to show signs of weathering and staining. Concrete spalling also started to appear on sections of the building’s exterior, and the original colours had faded significantly by late 2022.
The Bel Air body corporate committee engaged Asset Project Management (APM) director, Adrian Butcher to set out a scope of works to refurbish and restore the apartments. Higgins Coatings was awarded the project and began the extensive nine-month repainting and remediation process in February 2023.
The challenge
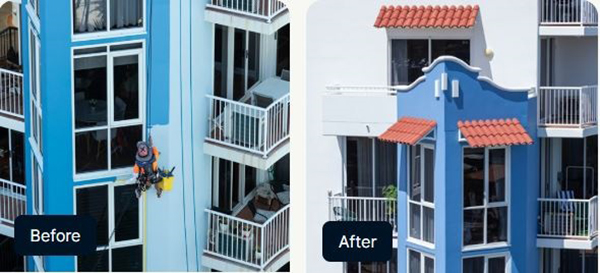
The restoration presented several key challenges to the project team, which required careful consideration of the system of products to be applied.
Access was a key challenge. The 20-storey towers have unique architectural features on the roof including spire-shaped turrets and a large decorative moulding around the perimeter that required sections to be replaced. As a result, the products required to repaint the exterior needed to accommodate the access challenges by being able to be applied using a combination of spray, roller and brush.
The works also needed to be staged to minimise disruption because the apartments were occupied during the refurbishment. David Murden, Higgins Coatings branch manager (Queensland), said this required careful planning and execution by Higgins and APM to deliver the project on time.
“With extensive experience in commercial repainting, Higgins Coatings were able to provide a comprehensive rope access plan to complete the job efficiently and with minimal disruption. Our team were also able to adjust the labour force as necessary, at times having up to 10 painters on site to successfully deliver this project,” Murden said.
Coastal consideration
Given the coastal location, the exterior surfaces needed high-performance systems that could resist salt air, high UV radiation and airborne dust and dirt from traffic.
Returning to heritage with colour
Careful consideration was required on the colour scheme. Given the apartments are a Gold Coast icon, the project team wanted to restore the exterior façade back to its original heritage colours, but in a more modern timeless manner.
The solution
APM's Adrian Butcher worked with Dulux Specification Manager, Casey Ngatai, who wrote the detailed specifications for the wide range of products and systems required to repair and protect the various substrates and provided full project support throughout.
Successfully tackling a complex façade restoration
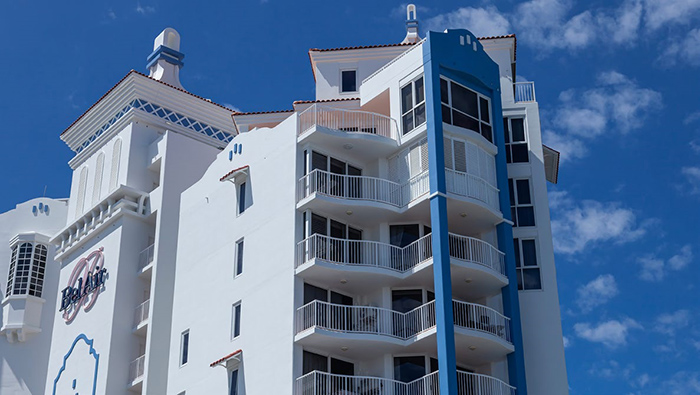
To resolve the concrete spalling issues on the façade, Emer-Patch Primer and Emer-Patch Repair were used to seal and restore. Since the structure is built with steel reinforced concrete, a high build protective elastomeric membrane coating of Dulux Acratex AcraShield was applied as the topcoat. With its anti-carbonation properties, it protects the steel throughout the concrete from corrosion. Dulux Acratex AcraShield is also weather resistant and has crack bridging capabilities, which can accommodate crack movement of up to 0.9mm (6 x DFT - Dry Film Thickness) to achieve long-term protection.
The tower spires, which are in constant sunlight, are highly prone to masonry cracking; therefore, another Dulux Acratex high performance elastomeric membrane was used, this time Dulux Acratex AcraSkin. With its leading crack bridging protection, AcraSkin can accommodate crack movement of up to 2.7mm (9 x DFT - Dry Film Thickness). Additional benefits of Dulux Acratex AcraSkin are its weatherproofing properties, high solids and high film build (300 micron in two coats), water resistance and vapour permeability, ensuring long-term exterior durability especially in this coastal environment.
Meeting the challenges of a coastal location and highly corrosive C5 environment
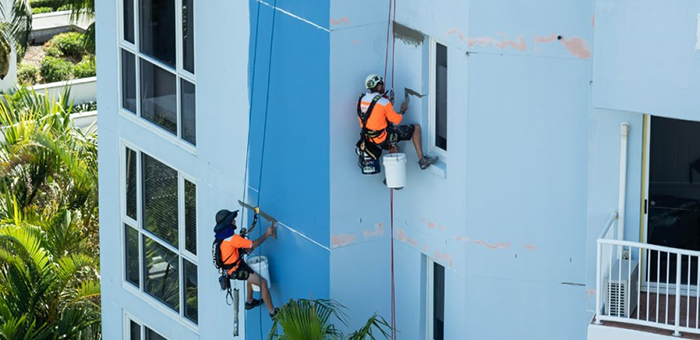
A high-performance protective coatings system was required on the Bel Air Apartments’ external steel substrates, which are exposed to the elements. A two-coat Dulux Protective Coatings system was applied to the aluminium awning frames, bollards and balustrades.
Dulux Durebild STE was applied as a primer. This highly versatile, two-pack, high solids, surface tolerant epoxy is a proven primer on suitably prepared steel and concrete.
Dulux Weathermax HBR was then applied as a topcoat. Weathermax HBR is a high build, recoatable polyurethane coating used over a wide range of suitably primed substrates, including aluminium. It exhibits excellent gloss and colour retention during extended service periods in severe marine environments and in extreme UV exposure.
This two-coat Dulux Protective Coatings system ensures longevity and maximum protection of the Bel Air Apartments’ substrate.
Colour advice & support
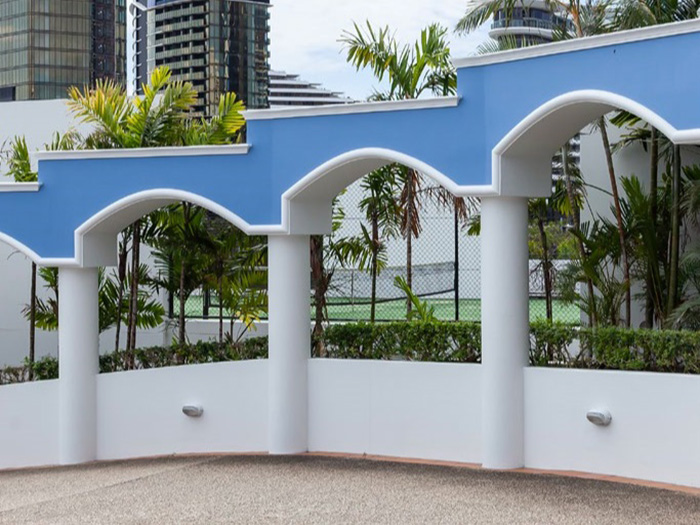
Dulux supported Asset Project Management and Higgins Coatings with colour advice and a variety of colour selections, providing onsite painted samples for the committee to make their final decision. Following the onsite trials, Dulux Mt Aspiring and Dulux Blue Fin were chosen as Bel Air’s main paint colours.
Project outcomes
APM’s Adrian Butcher credited Casey Ngatai's extensive product knowledge and excellent support for contributing to the success of this project and many others he managed over the years.
Dulux representatives also carried out regular inspections and issued project activity cards as the painting progressed.
"When I’m engaged by a client, I contact Casey to attend the site and write the specification. This positive relationship is vital to APM and our ability to deliver successful outcomes. Dulux issues independent reports to ensure the correct volume of coatings is being applied, and that allows the warranties to be signed. “I only use manufacturers that have an after-service program in case there’s a future issue. Dulux are very easy to deal with. In the rare case that there is an issue, they’ll work closely with us to ensure it is resolved quickly,” said Butcher.
“The Dulux support and service was integral in ensuring prompt delivery and supply of the large volumes of paint required for a job of this size and nature," Higgins Coatings’ David Murden added.
"The collaborative process between Dulux, Asset Project Management, Higgins and the body corporate is testament to the success of the refurbishment of this iconic Gold Coast project, and it was rewarding seeing the progress throughout the project to the completion," noted Casey Ngatai, Dulux Property Services Manager Queensland.
Delighted clients
Newly restored, the apartments are again showcasing the refreshed bright colours that complement their distinctive heritage architecture.
“The painters were all very polite and courteous, and the new colours came up beautifully. The committee is very happy with the results," said Wendy Drysdale, apartment owner and body corporate committee member.
Products specified:
Service area roller doors (Substrate: Painted mild steel)
- Dulux Protective Coatings Durebild® STE - PC237 Two Pack Epoxy
- Dulux Aquanamel® Gloss
Awning frames (Substrate: Previously powdercoated aluminium)
- Dulux Protective Coatings Durebild® STE - PC237 Two Pack Epoxy
- Dulux Protective Coatings Luxepoxy 4 White Primer Two Pack Primer
- Dulux Protective Coatings Weathermax® HBR Two Pack Gloss
Door frames (Substrate: Painted mild steel)
- Dulux Protective Coatings Durebild® STE - PC237 Two Pack Epoxy
- Dulux Protective Coatings Weathermax® HBR Two Pack Gloss
Hoods over service doors (Substrate: Painted mild steel)
- Dulux Protective Coatings Durebild® STE - PC237 Two Pack Epoxy
- Dulux Weathershield® Low Sheen
Rooftop spires (Substrate: Painted concrete walls)
- Dulux Acratex® AcraSkin® Low Gloss
- EMER Emer-Proof® Primer Non-Porous
- EMER Emer-Proof® Advanced
Main building walls, columns and EPS trims (Substrate: Painted concrete block, brick, masonry)
- Dulux Acratex® Green Render Sealer
- Dulux Acratex® AcraShield® Advance
Downpipes and other plumbing pipes (Substrate: Painted PVC)
- Dulux Precision® Maximum Strength Adhesion Primer
- Dulux Weathershield® Low Sheen
Louvres – timber (Substrate: Painted timber trim)
Exposed beams and rafters (Substrate: Painted timber trim)
- Dulux 1Step® Oil Primer Sealer Undercoat
- Dulux Weathershield® Low Sheen
Awning soffits (Substrate: Painted compressed fibre cement façade panels)
- Dulux Acratex® AcraPrime® Solvent-Based Clear
- Dulux Weathershield® Low Sheen
Car park pillars (Substrate: Painted concrete walls)
Slab edges and concrete soffits (Substrate: Painted concrete walls)
- Dulux Acratex® Green Render Sealer
- Dulux Weathershield® Low Sheen
Backing the experts
At Dulux, we leverage our deep expertise to support architects, interior designers, builders and engineers to design and build with confidence.
More than 100 years of experience and an unrelenting focus on quality and innovation allow us to back the experts with premium products, industry-leading service and trusted advice.
Project details
Project: Bel Air Apartments
Location: Gold Coast Highway, Broadbeach, Queensland
Client: Bel Air Apartments Body Corporate Committee
Project Manager: Asset Project Management
Applicator: Higgins Coatings
Project Scope: Repaint and remediation of three high-rise towers and common area
Products: Dulux Paints, Dulux Acratex®, Dulux Protective Coatings and EMER.
Year: 2023