
Building smarter: The advantages of modular and prefabricated homes
Modular and prefabricated homes are increasingly considered a solution for Australia’s housing crisis. With skilled labour shortages, operational and supply chain inefficiencies, and productivity, quality, and safety issues impacting housing delivery, modular construction methods offer a practical alternative to traditional construction.
At the recent Sustainability Summit 2024, a distinguished panel of experts drawn from across the architecture, design and building materials spectrum debated the merits and challenges of modular and prefab buildings, especially in the context of the national housing crisis. Moderated by architect, author and academic Tone Wheeler, Principal at Environa Studio, the panel featured Chris Hayton, Principal at Rothelowman, Richard Parkes, National Architectural Specification Manager at DECO, Jet Geaghan, Associate at Woods Bagot, Karl-Heinz Weiss, Consultant at WoodSolutions, Georgios Anagnostou, Studio Director at Studio Johnston, and David Hartigan, Executive Project Director at Case Meallin.
Tone Wheeler kicked off the discussion by recalling his student years back in the 1970s, when he had done a project on a ‘kit of parts’ house, or what we know as modular construction today.
Making a clear distinction between the VOLA and KOPA styles of prefab construction, he says, “VOLA is volume assembly. VOLA is when you take a whole building or a whole room or suite of rooms and that's prefabricated in a factory.”
“That's what most people understand by modular construction or prefab but there's also prefab, which is a kit of parts assembly (KOPA), a series of panels, walls, floors, whole sides of buildings if you like, which are prefabricated in a factory, then taken to site and assembled.”
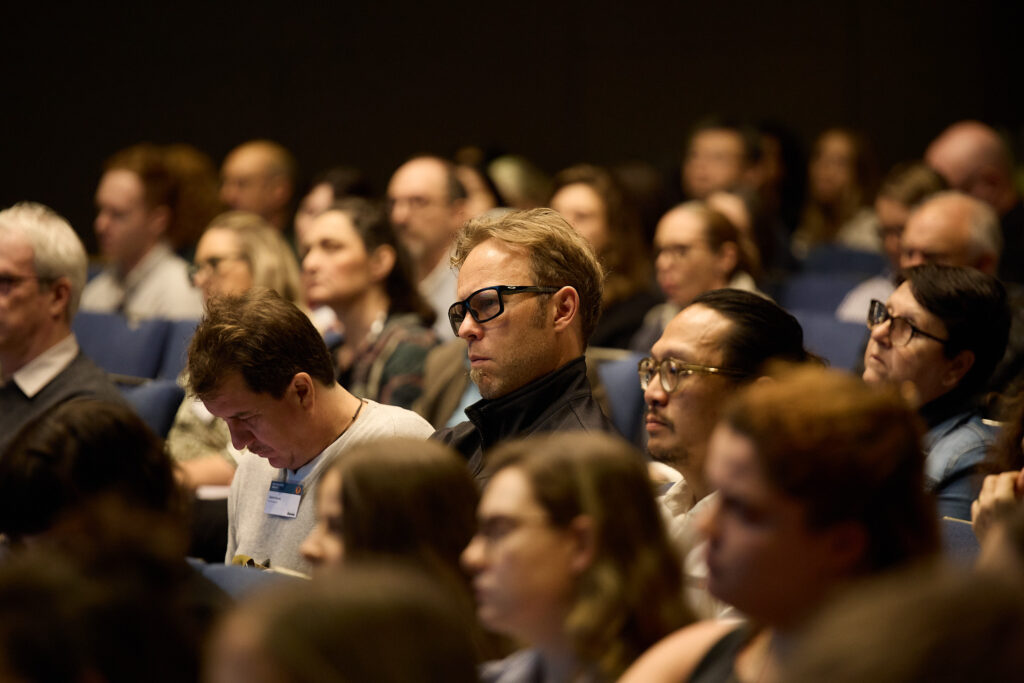
Is prefab the solution to Australia’s housing crisis?
Chris Hayton, whose firm, Rothelowman is involved in an enormous amount of housing across Australia, believes it is. “There's a problem as we all know in delivering that housing at the moment and quite simply I see prefab as part of the solution.”
Hayton also flagged the barriers that restricted the adoption of more modular or prefab construction, particularly how the design industry was trying to fit prefab systems to old ways of building, and highlighted the need to optimise the system to deliver better outcomes.
Presenting a manufacturer’s perspective, Richard Parkes from DECO saw modular construction as “the future of where we need to be to be able to achieve sustainability and to achieve the volume of growth that we need to be able to house all the people that are in Australia as well”.
Factors such as the speed of manufacture, the ability to create offsite and install it onsite as well as the potential to recycle were some of the factors that drove his passion for the prefab industry.
Volume assembly or kit of parts – which prefab style is better?
Jet Geaghan drew on his experience with Woods Bagot, which designs and delivers an extensive amount of housing around the world, and also works on different scales of projects where prefab of both volumetric and kit of parts styles is used extensively and very successfully.
While it’s sometimes called Design for Manufacture and Assembly (DfMA) or Modern Methods of Construction, Geaghan observed that prefab – preparation of things in factories and then being assembled on site that can be also disassembled – wasn’t that modern.
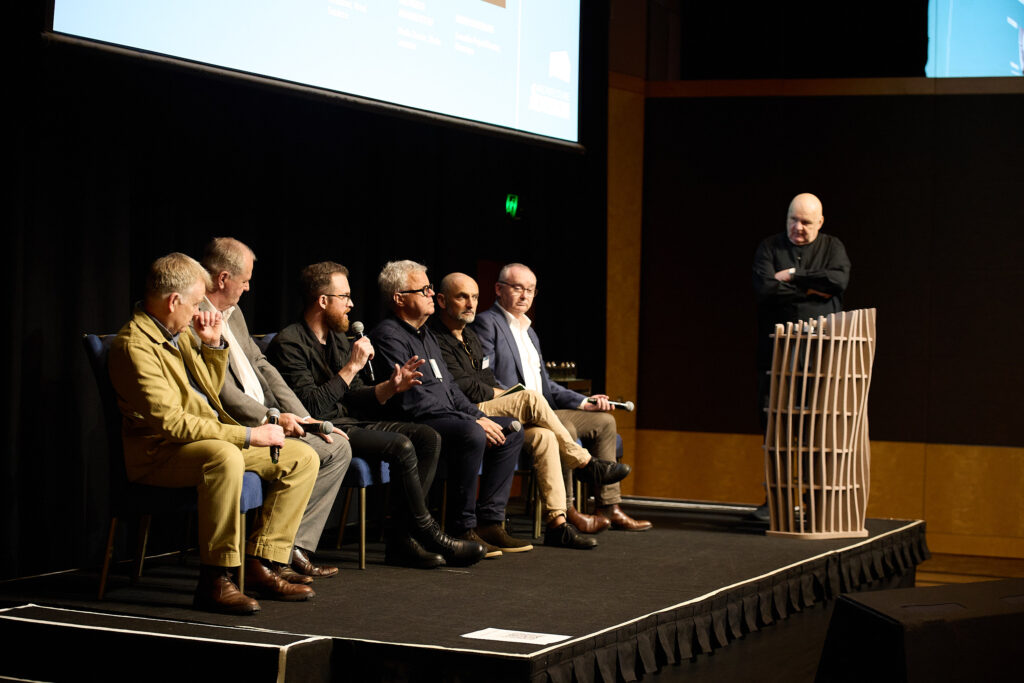
“It's used in all classes of buildings and it is taken up by builders and the construction industry to speed things up because everyone knows that a faster program is a more profitable one,” he says.
However, Geaghan is not a fan of the much-vaunted volumetric approach, which he equated to “transporting air on the back of a truck”, calling it not very efficient.
Woods Bagot has been researching how to use prefab in the delivery of dozens of schools in New South Wales, and also implementing it in housing.
“We've come back to that kit of parts approach, and we're realising we're already using it in unitised facades, fitouts and what not, and now we've just got to get the industry to start taking on the bigger challenges of prefabbing things like structure and the bigger parts of buildings, and that's what we're still investigating, and we've got a lot of work to do,” Geaghan says.
Speaking of the prefab system, WoodSolutions consultant Karl-Heinz Weiss, who describes himself as a cabinet maker who “moved from cabinets to bigger cabinets” made an interesting comparison of prefab construction methods to IKEA’s modularised operating model. System 32, he explains, is a design principle used by IKEA to create their furniture and cabinetry, and refers to the 32mm distance between two holes of 5mm diameter centre to centre.
Weiss, who is renowned for his pioneering work with engineered timber as well as a strong commitment to advancing DfMA and Modern Methods of Construction, referenced the IKEA example to highlight the importance of systems and system thinking in modular buildings.
On a similar note, Georgios Anagnostou from Studio Johnston whose interest in prefabrication comes from his background in carpentry and timber engineering, cited the example of timber-frame houses to compare traditional building systems to the modular approach.
“They were all based on modular items and measures,” he says, “and I see this now as just another further natural progression that we're moving into – another realm of prefabrication from a kit of parts to panelisation to the volumetric module.”
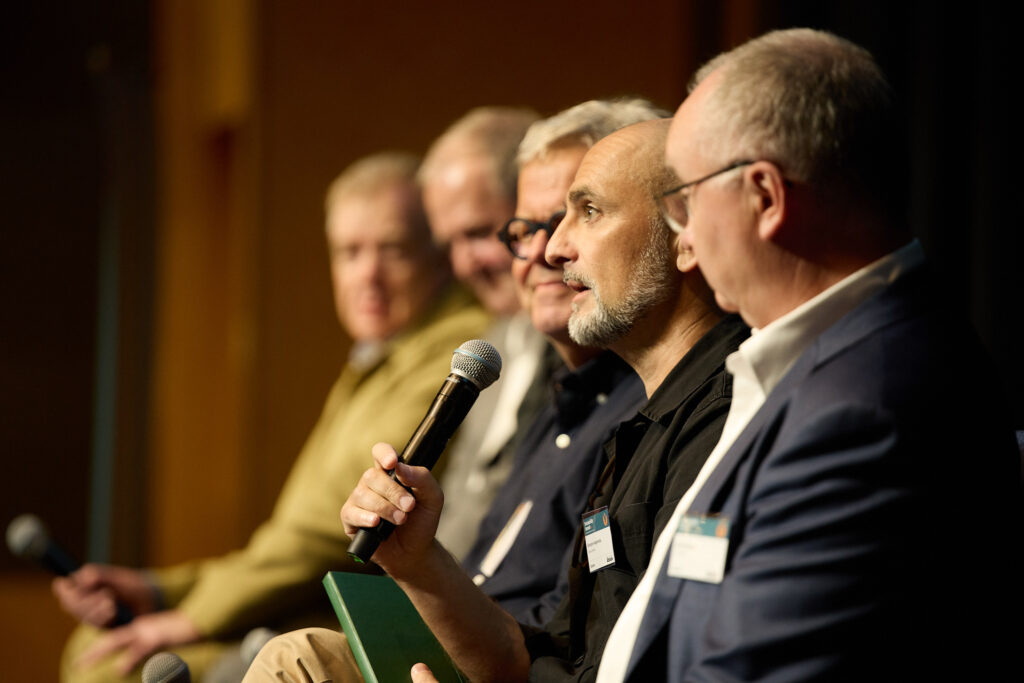
Anagnostou also had an interesting take on whether pre-manufactured modular design can help and fix the housing crisis. “I think it also works the other way around. The housing crisis can be a catalyst to help fix our inefficient construction industry in a way,” he says.
Prefab housing – then and now
While the benefits of modular construction such as speed of delivery, lower costs, quality consistency, sustainability and scalability are understood better today, the situation was quite challenging in the early days of prefab, according to Case Meallin Executive Project Director David Hartigan who used to run a modular manufacturing business about 14 years ago.
“We were a little bit of a voice in the wilderness. There weren't too many people doing it. People didn't understand it. Architects, builders, clients didn't understand it. But one of the early houses that we built was here in Sydney. And, it sold at auction two weeks ago for $2.2 million. It was a 96-square-metre two-bedroom cottage.”
Interestingly, there was no discussion in the sales brochures about the cottage being modular. “It was just a quality house that went for a lot of money,” Hartigan says.
How modular/prefab construction can shape the future of housing in Australia
With the federal government putting $900 million on the table for manufacturing innovation in housing, there is tremendous opportunity for the modular and prefabricated construction industry to meet the demand-supply gap in the housing market while also addressing the shortcomings of the traditional building industry, which is hampered by skills shortage, project delays, sustainability challenges, construction waste, quality issues and more.
By combining technology and innovation, the prefab industry has the potential to create modular homes that deliver design flexibility, sustainability, quality, durability and cost savings, making them more appealing for modern living and more accessible to buyers across income groups.
The Panel Discussion "Can Prefab/Modular Fix Our Affordable Housing Crisis?" was just one ot the ten CPD seminars hosted as part of The Sustainability Summit in November 2024. The Summit is a day-full of CPD education targeted at Architecture and design professionals and those looking to expand their knowledge and expertise in sustainable built practices. Sign up for notifications of future events here.
- Popular Articles
Related Articles
Sustainability
Sustainability Summit Panel #5: Can prefab/modular fix our affordable housing crisis?
Modular and prefabricated buildings are gaining attention as innovative solutions to the challenges faced in the constru...
Sustainability
Designing dignity: Insights into the future of aged care design
At the Sustainability Summit, experts discussed transforming aged care facilities into vibrant, community-connected spac...
Industry News
Sustainability Summit 2024 in review
Having taken place at The Fullerton Hotel in Martin Place, Sydney on 14th November, the Sustainability Summit has wrappe...