
Off-site sustainability: The rise of prefabricated construction
Prefabricated construction is transforming Australia’s building industry by improving efficiency, reducing waste, and lowering carbon emissions. This article examines the sustainability benefits of off-site manufacturing and showcases how companies like AWS are enabling smarter, faster, and more environmentally responsible construction solutions.
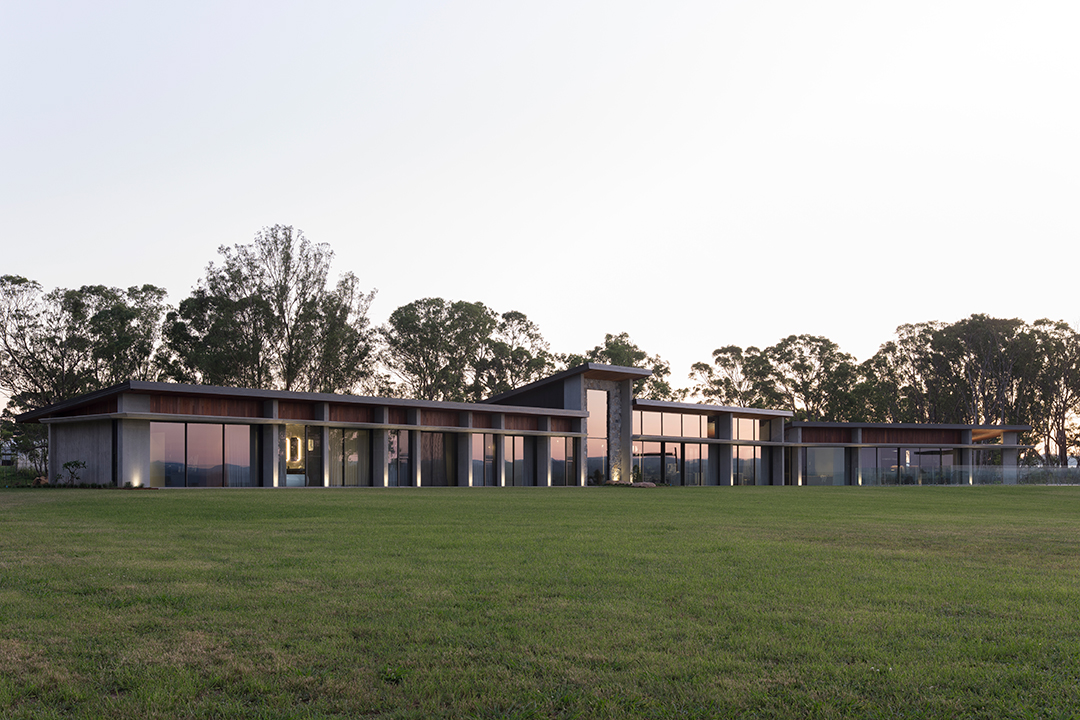
A building site without the constant roar of machinery, the endless deliveries, and the overflowing skips of waste? This isn't a utopian dream – it's the reality of Australia's prefab revolution. For decades, the rhythm of our construction has been largely defined by the chaotic cadence of the on-site assembly, and this conventional, largely reliant approach has shaped our built environment with inherent limitations.
Exposed to Australia’s volatile weather patterns, logistical complexities that spill onto neighbouring streets, the ever-present challenge of skills availability and blown-out project timeframes, and the excessive waste produced on site, there are multiple reasons traditional construction methods are facing a reckoning. And as their effectiveness and environmental implications are being brought into question, a powerful force is gaining momentum: prefabrication and industrialised construction.
In truth, this shift has been underway for a few years. But now, the construction industry is finally entering an era where architectural ambition meets unprecedented building efficiency, promising faster project timelines, reduced environmental impact and enhanced quality.
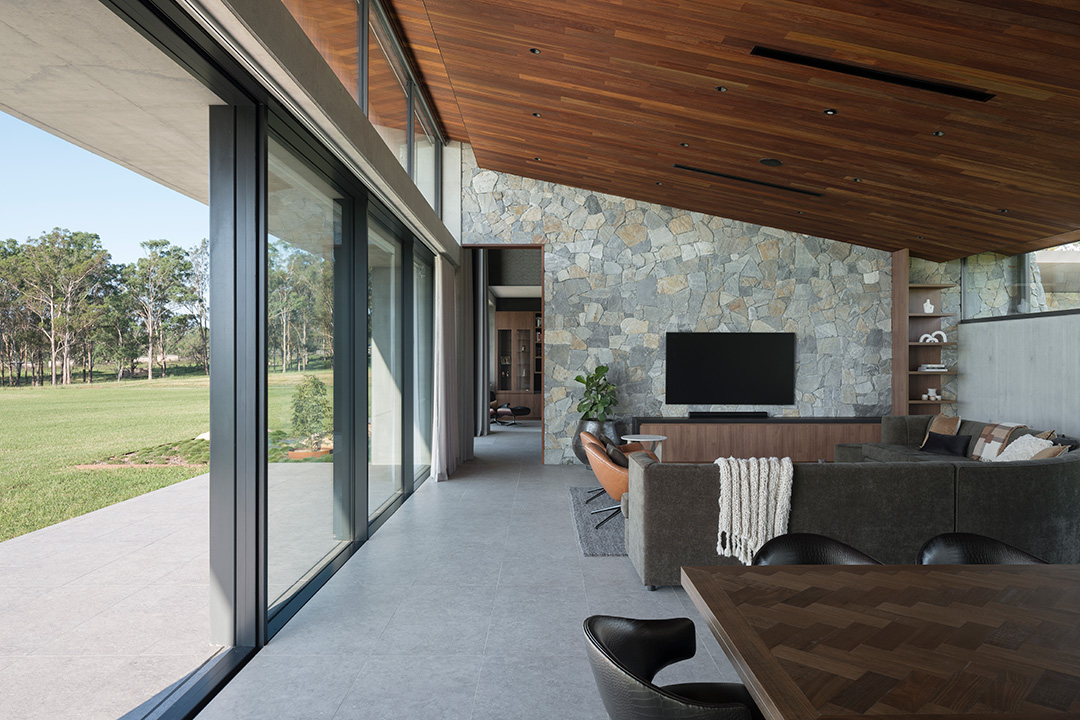
Overcoming limitations of conventional construction
Once considered a niche approach, off-site manufacturing is rapidly gaining traction, propelled by a confluence of factors including the urgent need for more affordable housing and an ever-increasing emphasis on environmentally responsible building practices. The rise of prefabrication is promising a particularly compelling vision for the future of the built environment, and some of the case studies from the last few years clearly demonstrate this potential.
Take Mirvac’s Tullamore pilot in Melbourne, which saw the developer build four dwellings using conventional construction methods and four identical homes using prefabricated wall and floor panels. Unsurprisingly, the prefabricated programme turned out to be 23% faster and reduced both labour hours by 11% and high-risk work, like scaffolding, by 42%, creating a safer and healthier construction site. Plus, on-site waste was decreased by an impressive 50%, and off-site manufacturing helped eliminate six weeks of traffic that would inevitably affect the local community.
These numbers prove that the dynamic shift towards industrialised construction is not just a trend that can speed up project timeframes – rather, it represents a fundamental rethinking of the industry that offers a pathway to a more resilient and sustainable built future. So much so that industry reports indicate a substantial increase in the adoption of prefabricated construction methods in the coming years, with the market poised to reach an expected output of $22.28 billion by 2028.
Here, we explore some of the environmental potential of prefabrication and look at how leading manufacturers of high-performing façade and window solutions, like Australia’s own Architectural Window Solutions (AWS), are embracing – and enabling – this shift.
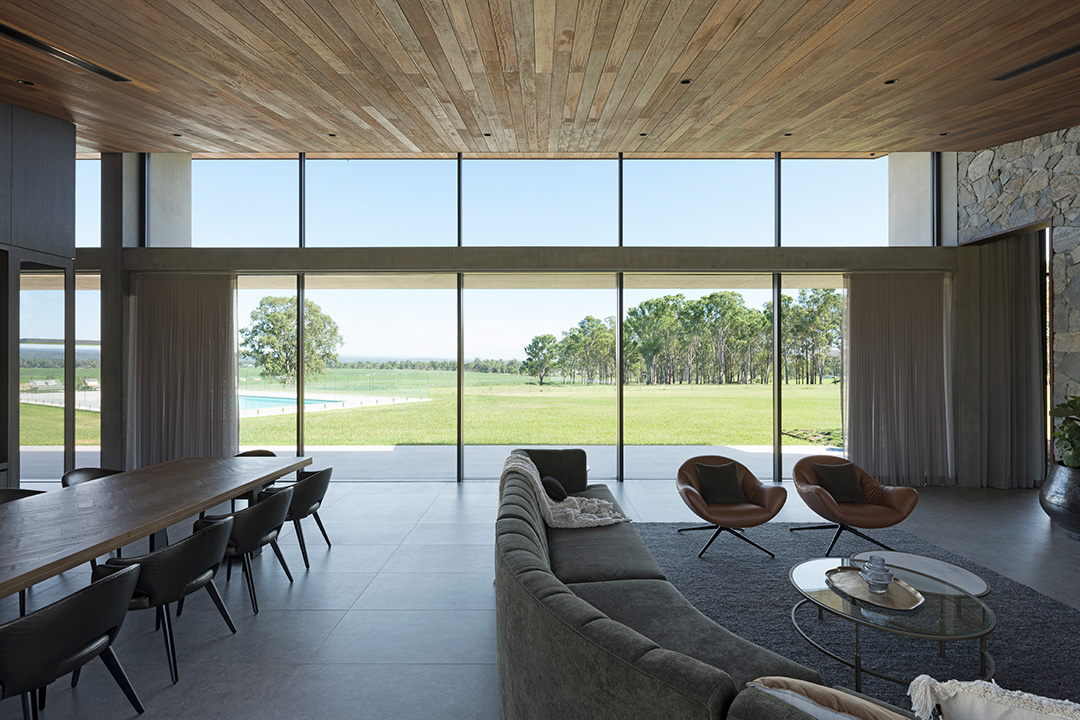
The benefits of prefabrication
There is no doubt that the growing popularity of industrialised construction is linked to its inherent sustainability advantages. In a sector traditionally associated with significant waste generation and high carbon emissions – while statistics vary, conversely, according to industry figures, almost 40% of Australia’s waste comes from the construction and demolition sector – prefabrication presents a powerful alternative.
By shifting construction activities to controlled factory environments, the industry can achieve unprecedented levels of material efficiency, reduce on-site waste sent to landfill, and optimise the use of resources. Plus, the precision inherent to factory-based production directly contributes to the enhanced performance and longevity of buildings, while rigorous quality control measures that ensure prefabricated components are manufactured to exacting standards help create more energy-efficient, enduring structures with reduced operational energy consumption over their lifespan.
Naturally, with this shift in motion, it’s paramount for manufacturers and suppliers to embrace the potential of prefabrication and off-site manufacturing. And AWS – Australia’s leading suppliers of aluminium window and door systems – emerges as one of the essential enablers of this transformation.
“The shift toward industrialised construction, modular prefabrication, and factory-built components is revolutionising the built environment,” enthuses Murray Chaloner, AWS Product Manager. “And our high-performance windows, doors and façade systems are designed to seamlessly integrate into off-site manufacturing processes, ensuring greater efficiency, reduced waste, and faster project completion.”
Designed to support modular design approaches that enhance sustainability outcomes, AWS’s aluminium systems are inherently aligned with these principles, and their meticulously manufactured solutions embody the very concept of precision engineering, which contributes to more efficient assembly – both within the factory setting and on site.
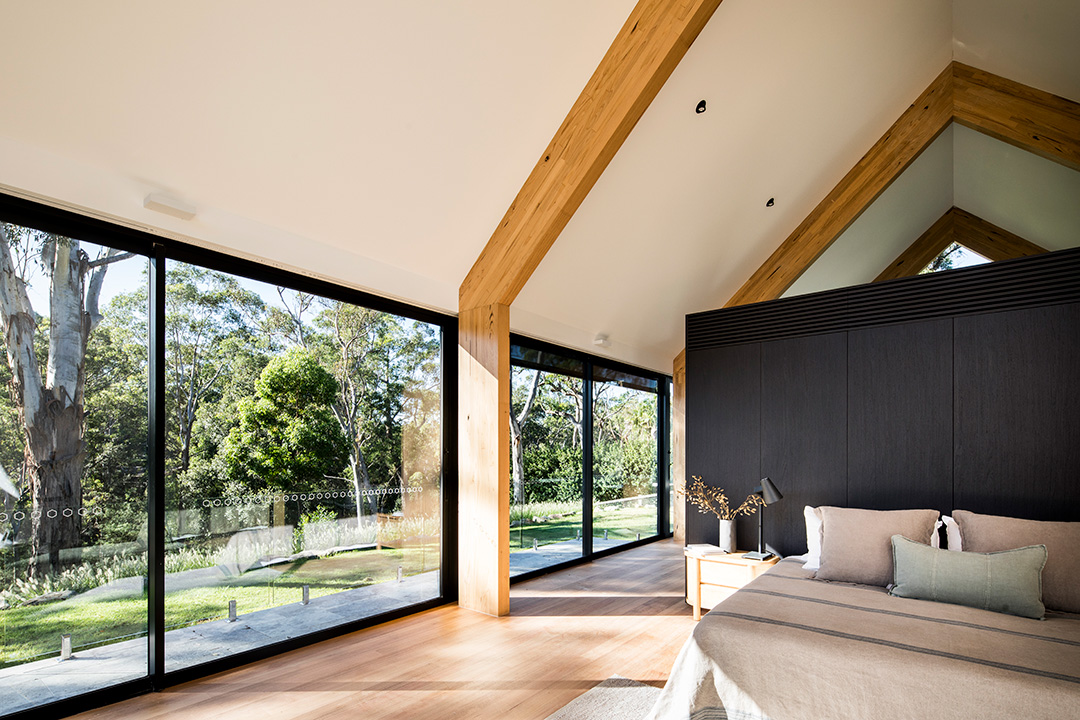
Pre-assembled systems for better post-installation performance
But this rigorous manufacturing ethos doesn’t just speed things up – Murray adds that AWS’s prefabricated façade panels and window systems offer a superior pathway to achieving high-performance building envelopes.
“The stringent conditions of factory assembly allow for meticulous installation, which is assisted by a multitude of AWS-designed adaptors specific to modular buildings with various wall thicknesses and façade elements that ensures consistent airtightness and optimal thermal performance, absolutely critical to achieving weather tightness, energy efficiency and occupant comfort.”
An excellent example of this potential is an 8-star thermal-rated compact modular dwelling in Wonthaggi, Victoria. Designed by Ecoliv Sustainable Buildings to complement its stunning Victorian surroundings, this one-bedroom weekender was prefabricated in a factory setting and incorporated high-performing AWS solutions.
AWS’s custom-made Series 504 Sliding Windows – used all throughout the dwelling to maximise natural light and ventilation – enabled designers to prioritise energy efficiency, while the integration of double-glazed openings, like the MAGNUM™ Series 618 Sliding Door, seamlessly connects the indoors to the outdoor deck and contributes to the home's impressive thermal rating. Plus, in terms of waste reduction, this modular dwelling’s prefabrication process led to a remarkable decrease in construction wastage by up to 52%, poignantly exemplifying the potential of modular prefabrication on multiple levels.
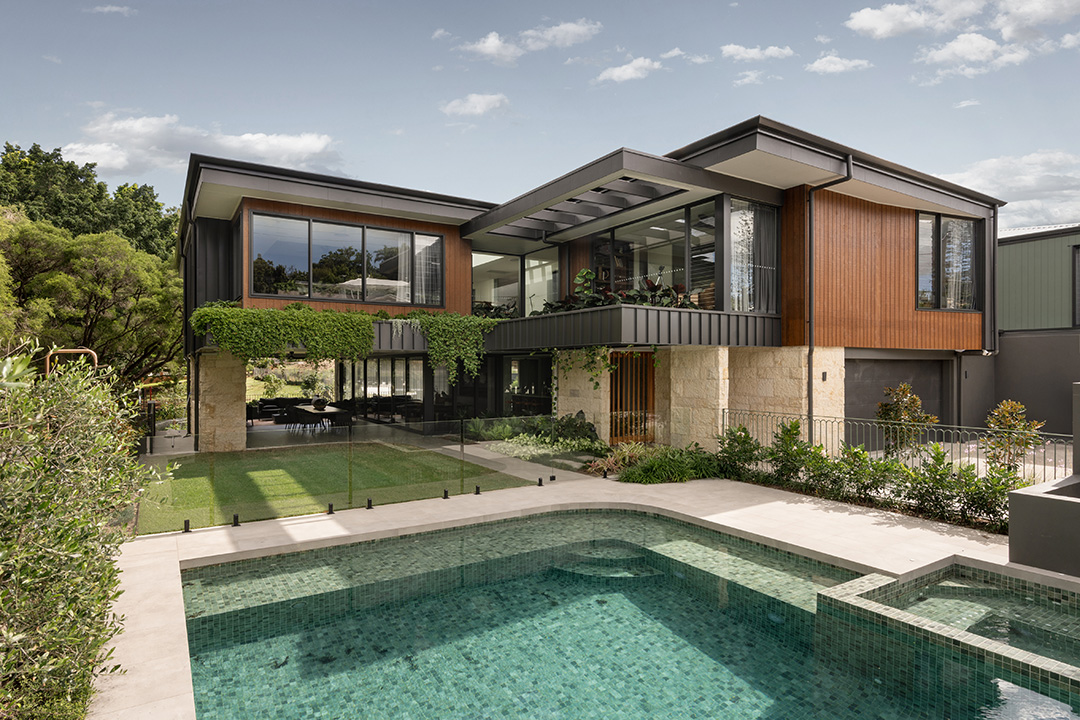
Efficient construction for lower embodied carbon
Another benefit of industrialised construction is its potential to lower embodied carbon, a particularly big-ticket item on construction’s environmental docket. By shifting a significant portion of the construction process to off-site manufacturing – reducing the need for material and workforce transportation, minimising on-site labour requirements and limiting the need for energy-intensive reworks – prefabrication can significantly drive down the carbon footprint associated with on-site activities.
AWS recognises embodied carbon as a critical aspect of sustainable construction by not only offering efficient, high-performing systems that seamlessly integrate with modular and prefabricated solutions but also by designing these precision-engineered products with material optimisation in mind. “We ensure that aluminium – a lightweight, highly recyclable and robust material – and other resources are used efficiently throughout the production process,” explains Angela Bevitt-Parr, AWS National Marketing Manager.
This considered approach to resource management not only reflects AWS’s own environmental commitments but also further contributes to lowering the embodied carbon footprint of the buildings in which our systems are integrated.
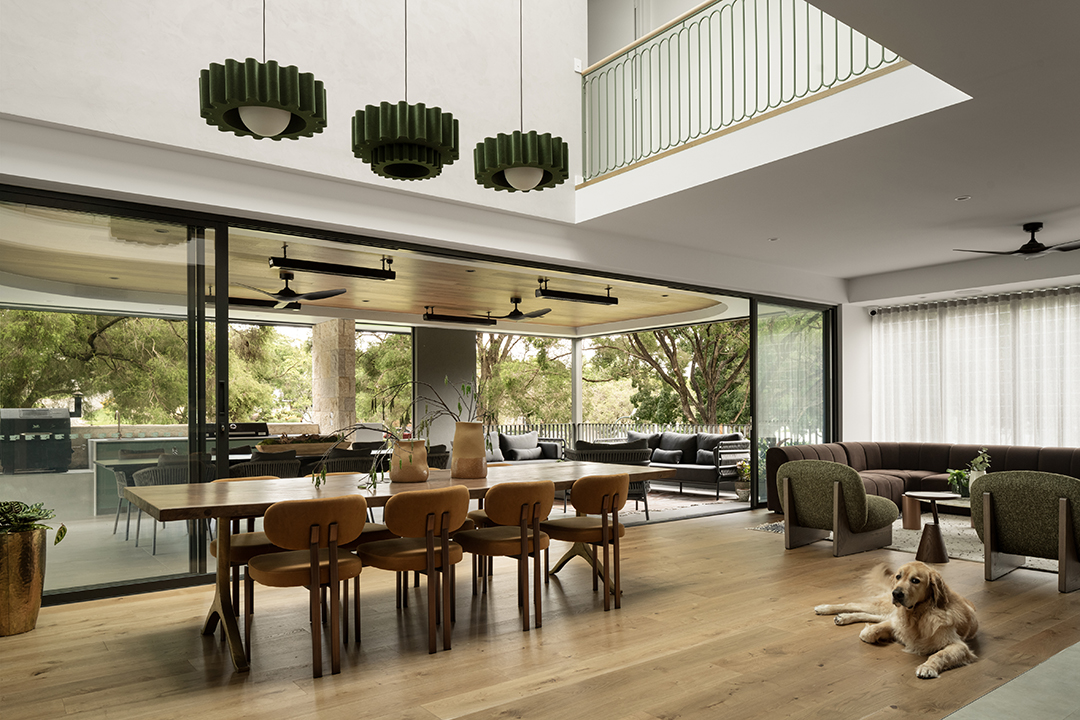
The future of sustainable construction is happening off site
Modular prefabrication and industrialised construction will undoubtedly play a crucial role in creating a more resilient built environment, and with their unwavering commitment to efficiency, precision, material transparency, circularity, and decarbonisation, AWS emerges as one of the leaders actively enabling the transition towards a more environmentally responsible future. These efforts are also underscored by AWS’s commitment to designing, manufacturing and assembling all their systems locally. This Australia-made ethos ensures a more reliable supply chain and more efficient delivery timeframes, and guarantees that all AWS products are carefully engineered to meet Australia's rigorous standards and unique environmental conditions, providing architects and builders with the assurance of quality and performance tailored to the local context.
With industry leaders like AWS, we’ll be seeing more and more construction sites where efficient, precision-engineered, high-performing prefabricated modules arrive on time, seamlessly slotting into place with minimal noise, waste and impact on the environment – and ensuring optimal energy performance from the moment they're installed. This is the promise of prefabrication and industrialised construction – a streamlined, efficient process that minimises environmental impact and maximises quality. And as Australia embraces this shift, AWS is not just building components; it’s helping industry professionals create a more sustainable, resilient, and efficient future – off and on site.
- Popular Articles