There has long been a stigma against modular (or prefab) building methods, especially in Australia. Despite modular construction’s ability to solve several problems — construction waste, rising cost of staff and materials, and weather-related delays, to name a few — many people have the misconception that prefab is synonymous with “low quality”.
Part of the reason is perhaps the association with demountable buildings, often found in schools or on work sites, which are typically used as temporary structures. Some people may also conjure up images of manufactured homes, which were previously used as low-income housing, particularly in the US, with the 1970s signalling the start of the manufactured housing boom.
At the time, manufactured homes were not required to follow the same building codes as stick-built (or “traditional”) homes, which resulted in several issues including leaking exteriors and poor heating systems. Homeowners were facing so many issues that new standards were introduced in the 1990s, forcing modular homes and buildings to follow all the same codes and criteria as stick-built structures.
Decades later, modular construction has advanced, resolving many of its earlier issues with strict standards and state-of-the-art technology. As a result, modular builds remain somewhat popular in the US and even more so in some parts of Europe, with most Swedish houses including prefabricated elements, for example.
Yet according to research from the University of South Australia, modular construction and prefabrication represents only three percent of Australia’s construction industry.
The cost of labour and materials is constantly rising, and builders often go bust, leaving projects unfinished. Quality issues are also rampant, and in certain parts of Australia flash flooding and extreme weather events are becoming increasingly common, causing construction timelines and budgets to blow out.
So, what can we do? Transitioning towards more modular methods of construction is one way that we can address some of these key issues, no matter the build type. It also gives us the opportunity to reduce construction waste and implement more ESD principles in our builds.
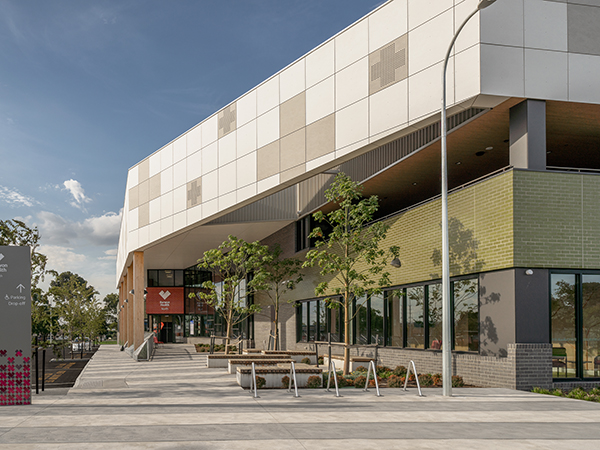
Above: Barwon Health North, a Geelong-based urgent care centre designed by Billard Leece Partnership. Equitone panels were used on the exterior facade to add a modern touch to the building while also providing durability and weather resistance / Supplied.
“As the planet is running out of resources, it is critical that the materials we use for construction should be designed and manufactured to achieve the concept of circularity,” says Cedric Pinto, Senior Specification and Sales Manager at Equitone South Australia.
“Lightweight and modular construction is the key for circularity, and it is seen that these construction techniques are being favoured, particularly in aged care and education projects.”
According to Equitone, 40% of the world’s greenhouse gases come from the construction industry. To avoid contributing to this, the company has created a through-coloured facade material, Tectiva, which works well with modular construction and has Cradle to Cradle certification. This means the panels can be recycled at the end of their life cycle, ensuring they don’t end up in landfill.
The panels allow the creation of a ventilated facade, which helps prevent the formation of moisture, condensation, and mould, making buildings a healthier place for people to live and work. Having a ventilated facade also significantly reduces or eliminates the need for exposed sealing or caulking, making the facade lower maintenance.
An example of these panels in use is in Barwon Health North, a Geelong-based urgent care centre designed by Billard Leece Partnership. Equitone panels were used on the exterior facade to add a modern touch to the building while also providing durability and weather resistance. Overall, the design represents the amalgamation of functionality and aesthetics, creating a welcoming and healing environment for both patients and staff of the clinic.
Another company very much focused on sustainability is Xframe, which produces a circular economy wall framing solution that allows spaces to be adapted over time without creating waste.
“Traditional building fit-out systems (think plasterboard lined walls with light gauge steel frames) are not designed to be easily adapted over a building’s life,” says Ged Finch, Chief Technology Officer, and inventor of the Xframe system.
“This means that when a change is required, the materials are either recycled, or as is most often the case, sent to landfill. In both situations, the value of the materials is lost and significant energy must be expelled to reprocess the waste into new products. In a circular economy, the products are instead designed to maintain their value through use cycles.
“Xframe achieves circularity through being designed for disassembly. We create a self-braced and self-squaring structural frame upon which clip-on clip-off linings can be reversibly attached. At end-of-life, all elements can be removed efficiently and without damage, allowing for direct reuse.”
According to Xframe, its solution is particularly well-suited to aged care spaces, as they are subject to constant change and varying market conditions. The Xframe system offers aged care providers the ability to adapt multi-room hospital and village accommodations in short time frames and with little disruption. It also makes it possible to quickly replace damaged linings between tenants, while offsetting the carbon and energy emissions that typically result from these processes.
Another framing system worth looking into is Caroma’s Modular Frame System (CAMFIS). According to the company, CAMFIS is the only modular bathroom frame that is available with sizings for popular Caroma Care products and produced at scale for cost efficiency, rather than hand built.
“With the cost of building materials and labour escalating faster than ever before, coupled with skills shortages constricting productivity in Australia, there is enormous pressure on those in the construction industry to search for innovations in systems and processes to help keep up with the ever-growing backlog of new building consents,” says David Cole, Senior Manager – Commercial Marketing at GWA Group.
“Prefabrication has for a long time proven to be an effective and reliable way to speed up the construction process with limited additional labour and skills input. In the plumbing industry, prefabricated bathroom pods have emerged as a growing force in construction projects and a major contributor to improved productivity.”
According to Caroma, CAMFIS enables plumbers to run their own prefabricated production lines to help solve their labour crisis and drive growth.
“By simplifying the prefabrication process down to pre-roughed in-wall units that support and connect Caroma bathroom products, plumbing businesses can install and fit off bathrooms in commercial applications with reduced on-site labour,” adds Cole.
“With prefabricated assembled frames delivered to their door, plumbers can rough-in prior to site delivery on a standardised frame in factory conditions, deliver to site, and then simply click them in to minimise on-site labour, reduce costs and alleviate the headache of coordinating on-site personnel.”
Reducing time (and therefore costs) is certainly an oft-mentioned benefit of modular construction, and that includes specialised modular builder, Modscape.
The company was selected as the modular provider for a 30-bed residential rehabilitation facility in Corio, Victoria, designed in collaboration with the Victorian Health Building Authority and Vincent Crisp Architects.
Situated on a five-acre site, the facility features bright, open spaces designed to promote relaxation among the residents, who are there to receive treatment for drug and alcohol addictions. Outdoor gardens and recreational areas connect seamlessly with their natural surroundings, while a sweep of eucalyptus trees adds to the facility’s serene setting.
According to Modscape, the use of modular construction techniques allowed the facility to be completed faster than traditional methods, without compromising on quality. The project is exemplar of the impact of well-designed spaces on rehabilitation, providing residents with the comfort and support they need to rebuild their lives.
In a similar vein, UnitingCare Queensland’s Sunrise Beach Aged Care Facility was designed to improve the lifestyle of its residents while also saving on construction time and costs.
“The design of the Sunrise Beach Aged Care Facility responds to ‘Person Centred Care’,” says Pino Gentile, Principal Architect at Thomson Adsett.
“Homes are designed to provide residents with an authentic domestic experience and are modelled in small clusters of 8-9 rooms. Each room is located around a series of light-filled courtyards, or alternatively provides views of the adjacent national park. Residents can easily access common areas and spaces to socialise or get food and drink from the house kitchen whenever they want to.”
The facility uses light gauge steel (LGS) framing made from Truecore steel (supplied by BlueScope), which is termite-proof without the need for insecticides, and is also highly resistant to tropical weather, meaning it won’t warp, twist, or shrink under wet conditions. These were some of the core benefits for client UnitingCare, as well as the fact that the use of Truecore steel LGS framing was able to significantly reduce construction time.

Above: Sunrise Beach Aged Care Facility uses light gauge steel (LGS) framing made from Truecore steel (supplied by BlueScope). Designed by Thomson Adsett. / Supplied
“[It] has allowed us to work around the limited onsite space,” says Mitchell Crisp, Principal of fabricator Ultimate Steel Framing, which also worked on the project.
“Smaller cranes were used, saving costs and positioning packs in out of the way locations. The ease of handling LGS frames meant labour could be split into smaller groups to work on multiple fronts, again helping accelerate the rapid progress of the job.”
As noted by Truecore, in a location where the demand for aged care accommodation is continuing to grow faster than most other parts of Australia, the timely provision of quality new homes for residents is crucial. Modular design represents a huge opportunity in this regard — not only in Queensland but nationwide, and in a wide range of applications.
Healthcare and aged care are just some of the build typologies that are leading the way in Australia’s modular revolution. This is a good start, and hopefully as people have more exposure to modular builds, we can start to chip away at the stigma around these “non-traditional” construction methods — and just maybe we’ll have a chance at addressing Australia’s growing housing crisis.
Main Image: Caroma’s Modular Frame System (CAMFIS) / Supplied
SUPPLIERS
BlueScope
Caroma
Equitone
Modscape
Xframe