Residential lifts have improved markedly in Australia over the last few years. And, as Deborah Singerman reports, they are now rising above simple functional requirements.
Lifts aren’t they all about whizzing people up and down multi-storey office blocks or high-rise
apartments? Well, not entirely. A lift, says Les Katz, managing director of Lift Shop, “lets you move people further away from sea level without climbing steps; it is a vertical train system designed to move people as quickly as possible vertically through a building”.
Like most members of the industry, he has worked with commercial lifts and what he calls “medical devices”, the more basic, low-rise platform lifts, or stair lifts with tracks for straight and curved, or wheelchair ramps. Home lifts, he says, were not viewed as “value adding to property” but more often as “eyesores”.
This began to change in 2002 with the release of AS/NZS 1735.18 Lifts, escalators and moving walks – Passenger lifts for private residence – Automatically controlled, a standard, Katz says, “that allowed us to do things differently, essentially compromise”. In Katz’s case this has meant focusing on “this new, third space” as “a home elevator specialist, an entirely new niche” that sets them apart from big commercial operators and smaller companies and franchisees.
With the August 2011 Productivity Commission report into Caring for Older Australians emphasising that most of our ageing population want to stay in their own home for as long as possible, residential lifts offer people more options, says Katz. For example, they give greater independence for people who, say, are not disabled but perhaps have a “gammy leg” and worry about going up and down stairs (though home lifts’ gamut of uses includes helping young parents with babies, he says).
The industry is new and there are no official statistics but Katz believes the market for residential lifts is growing 15 to 20 per cent a year.
Professor Shane Murray writing on housing the baby boomers in Beyond Beige: improving architecture for older people and people with disabilities (published in March 2008 by the then Royal Australian Institute of Architects) talked about the conditions of performance of a dwelling including “the structure of our family units ... and how much mobility we require”.
Over the last few years Guy Luscombe, head of aged design at Rice Daubney, has noticed that more home lifts, smaller type, discreet, European-style and using less floor space than a stair, have become available in Australia. There have been the changes to standards, regulations and compliance (including Part E3 Lifts in the Building Code of Australia) and to accessibility and mobility requirements generally, and you have lifts, Luscombe says, that are more than just functional.
“Design tends to try and say, ‘this is not just about regulation’. Design is not just being there. It’s about being better so it doesn’t stick out and be ugly but is actually seen as becoming part of something within the whole environment.”
What should you be looking for when choosing a residential lift?
According to Katz, there are three steps: the intended use; how it is going to fit into the building; and personalising the lift.
Mass movement (commercial) and quick, standard-box, post-heart attack, uses, for example, are at the ends of the spectrum, “but if you are 50, intelligent and realistic and plan to live in your house for a long time, have great sea breezes and a view from the top floor of a three-storey home, and your architect wants to put a kitchen up there and bedrooms on the middle level, which is very common, and you want to protect your future, add value to the property with something that’s going to look good, that’s only going to take a small amount of space out of the home’s living area, that’s going to be reliable, well priced and a very good ongoing service cost, then you are in the home elevator space.”
Speed, space and safety are crucial considerations.
“Everything around elevators is dead space, the ropes, cables, tracks, so you want to ensure maximum efficient and usable internal floor space as opposed to shaft space,” Katz says.
Lift Shop’s wheelchair lifting platforms carry up to four passengers - the United Kingdom-made P1, travelling up to one metre, and the Italian-made P2, up to two metres. The Elfo lift, Italy’s best selling swing door lift, is the fastest in its class at 0.3 metres per second, with a five- person capacity, customised Italian styles and finishes including frameless glass door options.
The latter are also new in 2011 to the Supermec, “the Rolls Royce of the industry”, says Katz. The Supermec 2 lift won the designEx 2011 best new product award for building technologies. Customised, it includes stylish finishes, popular minimalist stainless steel doors, costs around $55,000, taking six months in total from initial design discussions with Lift Shop, through the manufacture by Italian platform lift company, Elevatori Premontati, placement on site back in Australia and 6-14 day installation.
The lift has reduced headroom (2800 mm from top floor to finished floor level) and yet carries 630 kilograms (nine people). It is in its 10th year in the post-hydraulic traction market, an energy efficient more of operation where, Katz says, “a counterweight acts like a pendulum or scale balancing the lift so you do not need a big engine because you are lifting the weight of the people in that cabling, using only about 13 per cent of the power of a hydraulic lift.”
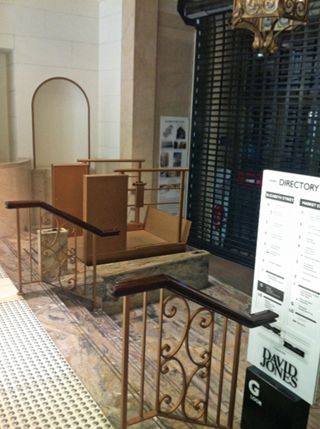
It is also the only residential lift to take full advantage of the new National Occupational Health and Safety Regulations (effective January 1 2012), which allows more flexibility, says Katz, including going faster, so rather than 12 seconds per floor (at 0.3 metres per second) the lifts can run at 6 seconds per floor (0.5 metres per second). Compare this with medical devices that can take 30 seconds to travel one floor; “nobody wants to be in a lift that takes that long,” says Katz.
Everybody, also, is scared of getting stuck in a lift. The Freedom Lift, manufactured in China and promoted for being easily fitted into existing homes (it costs under $40,000) and designEx best technologies winner in 2010, has an in-cabin emergency self-rescue button, which lowers the lift to the ground floor and unlocks the door if there is a power failure in the hydraulics. The Supermec continues to run even if there is a power outage because, says Katz, it is so energy efficient and has a fantastic battery system. The lifts also have a safety curtain, an infrared light beam barrier covering the full opening so nobody can get hurt.
“Remember, you are building the lift into your building,” says Katz of these long-term, integral propositions.