Stephenson’s Mill in Crookwell is exceptionally significant as a purpose-designed mill building built-in 1871 in a vernacular architectural style, using local bluestone walling 600mm thick.
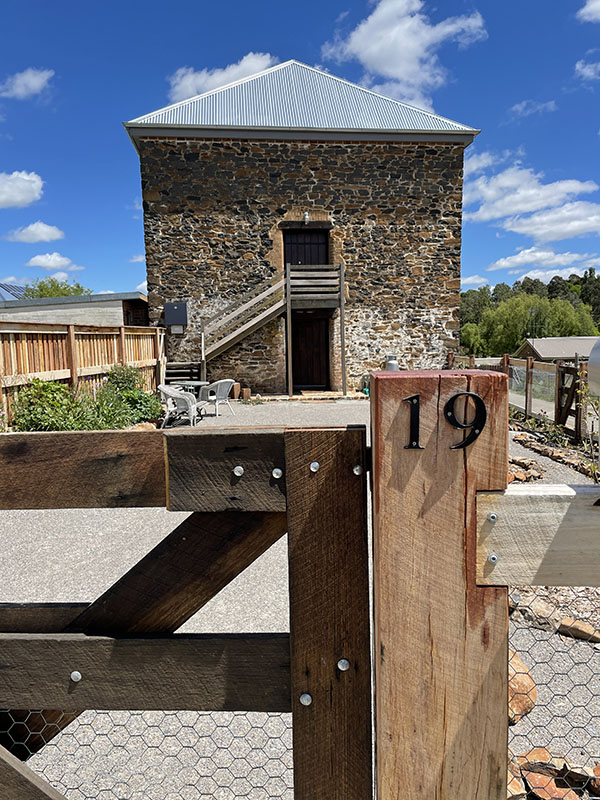
Employing the rarely used heritage incentives clause of the Local Environmental Plan leveraged public interest which lies at the heart of the provision. Zoned commercial, it is allowed to be used for residential use in return for conservation works to the historic fabric. This particularly enabled the retention of embodied energy, the first sustainability initiative. The second was the sealing of the envelope through new sarkings, new eaves linings, and new double-glazed window sashes in existing frames. A complete suite of low-tech energy systems was provided to address the harsh climate and local habits.

This project shows that having the will, imagination and skill makes for a kind of sustainability that is low-tech, energy-wise, and fitted to the needs of people and communities.
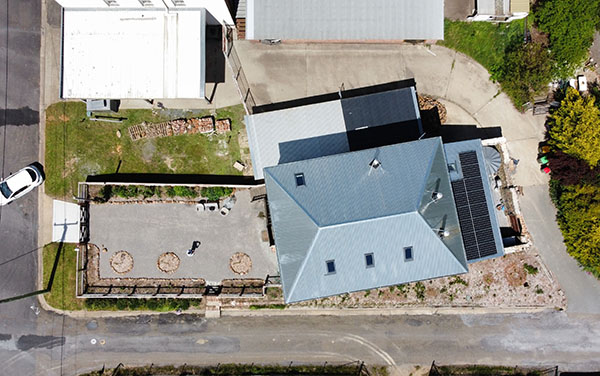
List all the sustainable products used in this build
- 5.32 KW Solar System incorporating LG Neon R380 Watt panels, also connected to Hot water heating system
- AAA-rated tapware & appliances throughout
- Re-use of 70-year-old recycled turpentine timber in the construction of staircase & balustrades to mezzanine level & front external stair balustrade restoration sourced from the demolition of the Goulburn Seifert Oval cricket grandstand 2020
- Re-use 80-year-old dry pressed bricks to envelope new rear access door opening to courts yard, bricks sourced from derelict farmhouse Gullen Flats Kialla NSW
- Re-use of various hardwood timbers throughout the renovation internally & externally, sourced from the demolition of existing water tank framing within the existing redundant roof structure listed for removal in the original scope of works
- Re-use of recycled light fittings, modified to comply with Basix commitments
- Re -use of Basalt sourced from the property at Gullen Flats Kialla NSW to replace & repoint damaged walls throughout the building
- Structural LVL beams sourced from sustainably grown trees substituted in the construction of the mezzanine floor framing in lieu of F17 native hardwood species specified in the original scope of works
- Re-use of second-hand doors & panelling to 50% of fit-out, sourced from various restoration outlets
- Recycled internal Oregon step tread extensions & balustrades to the existing staircase to comply with National Construction Code 2019
- Solid fuel combustion heating & cooking appliances throughout.
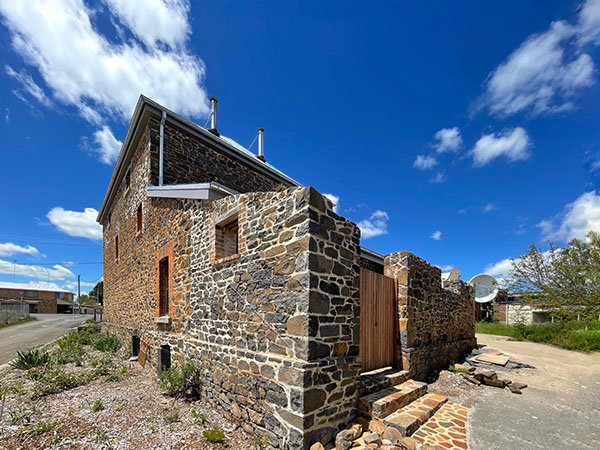

List all Local and/or State regulations that were met (or exceeded) in this project
- Section 81 Environmental Planning & Assessment Act 1979 including BASIX for housing
- Sub clause (10) “Conservation Incentives” clause 5.10 “Heritage Conservation” of Upper Lachlan Local Environmental Plan 2010
- Building Code of Australia
- Home Building Act 1989
- State Insurance & Care Governance Act2015
- S64 Local Government Act 1993
- S306 Water Management Act 2000
- National Construction Code-Plumbing Code of Australia
- Work Health & Safety Act 2011
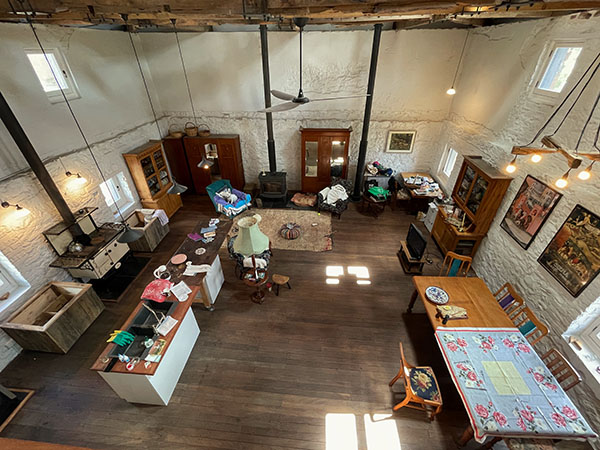
List all project green ratings that were met (or exceeded)
Since the project was small in scale, and the contribution of non-standard construction such as the 600mm walls was not able to be easily incorporated in standard Energy design templated models, we decided to use as the key measure the BASIX Certificate number: A296130. The sizing of the water tank, new solar power, and combustion heating system were each designed to suit the measurable needs of the project.
- Decrease energy costs
- Increase thermal comfort
- Decreased carbon emissions
- Increased the value of the asset
- Re invigorated a significant piece of heritage architecture for the benefit of the local & greater community
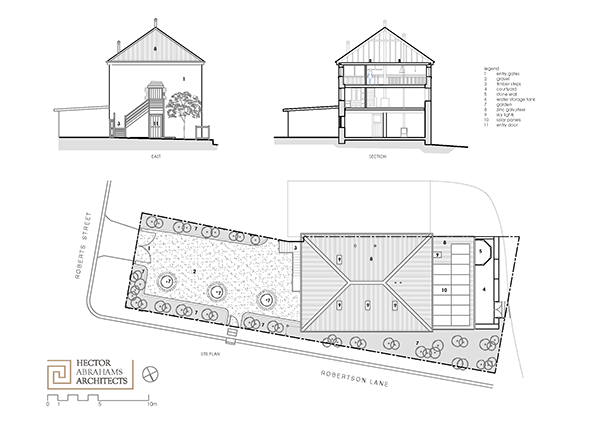
Sponsored by Bondor