Developed by Mirvac, 80 Ann Street is an iconic destination that will become an enduring benchmark for sustainability and energy efficiency. The new 35-storey development in the heart of Brisbane’s CBD is part of a large urban redevelopment project that aims to create a sense of livability while at work.
The building has been collaboratively designed to reflect a very ‘New Queensland’ workspace by offering superior connectivity and breathable spaces for improved wellness with abundant light, natural space and local greenery. The building features 60,000 square metres of premium-grade office space, more than 60 per cent of which has been committed to anchor tenant, Suncorp. Comprised of premium-grade retail space, the building aims to achieve a 6-star Green Star sustainability rating.
What was the challenge?
To ensure that 80 Ann Street could meet its sustainability targets, the building’s developers and architects needed to thoroughly test the building’s external wall components to be classified non-combustible in accordance with the National Construction Code (NCC).
It was important to ensure that the building’s 60,000-square-metre space could address the thermal, acoustic and fire-safe requirements without leaving any blind spots. Due to the scale of the project, the solution also needed to be easy to install and cost effective.
What products were used?
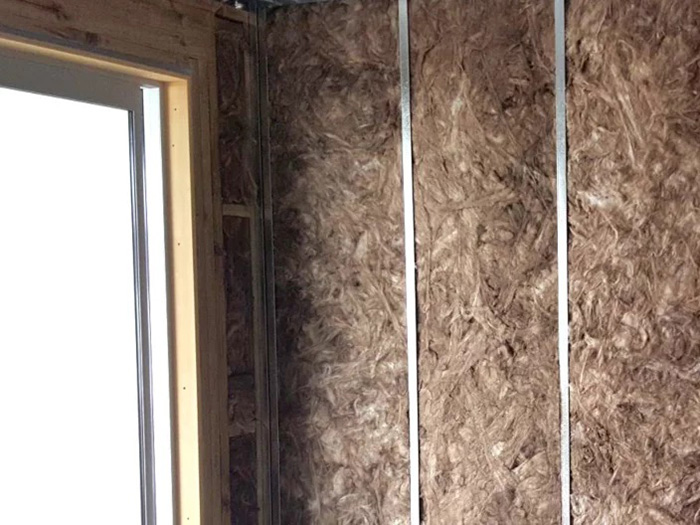
Knauf Insulation glasswool products were selected for their superior level of sustainability certification. Knauf Insulation’s glasswool products are manufactured with ECOSE® Technology using a binder that contains no added formaldehyde, phenols, acrylics, artificial colours, bleaches or dyes.
The binder has lower embodied energy than traditional glasswool and it is these sustainability properties that have made Knauf Insulation glasswool products the only products of their kind in Australia certified to Global GreenTag™ GreenRate Level A. This level of certification is instrumental in accruing additional credit points to ensure the project achieves the required 6-star Green Star rating.
Knauf Insulation 11kg/m³ acoustic partition rolls and Knauf Insulation 14kg/m³ acoustic partition batts were installed in the steel stud framed internal walls in addition to fire-rated and acoustical-rated plasterboard to achieve the required acoustic and fire-rated requirements for separating walls.
The exposed external concrete soffits with conditioned spaces above also required insulation to be installed to the underside of the concrete. This is traditionally accomplished using phenolic products laminated to a foil facing; however, this was not an option for the designers as the core insulation component was deemed combustible when tested to AS 1530.1. As a non-combustible solution was required in accordance with C1.9 (non-combustible building elements) of the NCC, Knauf Insulation worked with specialist laminator Ecolife Solutions to develop and test a modified version of the Knauf Insulation Earthwool® roof blanket, which was laminated to a non-combustible grey loom facing.
Both the insulation blanket and facing were not only deemed non-combustible when tested to AS 1530.1, but also tested to AS 5637.1 and achieved Group 1, further demonstrating the superior fire performance. Contractors Precision Interior Walls & Ceilings (PIWC) installed the product directly to the concrete soffit using standard insulation fasteners, with joins and edges taped in accordance with the installation method outlined in the AS 5637.1 test. The finished soffit consisted of an aluminium sheeting suspended from the soffit concealing the insulation.
Tom Fitzgerald from PIWC complimented Knauf Insulation’s level of certification, which supported the stringent sustainability and energy efficiency requirements of the 80 Ann Street development. “Knauf Insulation worked tirelessly to ensure we had a compliant specification for 80 Ann Street, which is targeting a WELL Certified, 6 Star Green Star, 5 Star NABERS Energy and 4 Star NABERS Water project. As a contractor, we are required to supply and install compliant materials project-wide and this is quite a task. Knauf Insulation provided ample supporting documents for all their insulation products, which helped ensure they were approved. Having all the current documentation in line with industry requirements stood out amongst their competitors.”
What was the result?
The installation of Knauf Insulation glasswool featuring ECOSE® Technology allowed 80 Ann Street to successfully achieve the required Green Star points while meeting the high acoustic performance and non-combustibility guarantee that is required to deliver a high level of fire safety and hazard mitigation.
“We were pleased with the products’ performance and intend to use the Knauf Insulation Acoustic products on future projects,” Tom said.
Kevin Bracken, General Manager of Ecolife Solutions, said Knauf Insulation’s one-of-a-kind Global GreenTag™ GreenRate Level A, ensured 80 Ann Street was well placed to achieve its 6-star Green Star rating.
“Knauf Insulation is also less itchy when handling the product and the high compression ratio made the delivery as well as the storage on-site a much easier task. This was greatly appreciated by all those involved in the process.”
Products used for project
The Knauf Insulation Acoustic range includes a selection of densities to provide builders, designers, installers and DIYers the opportunity to choose the best acoustic performance for their project.
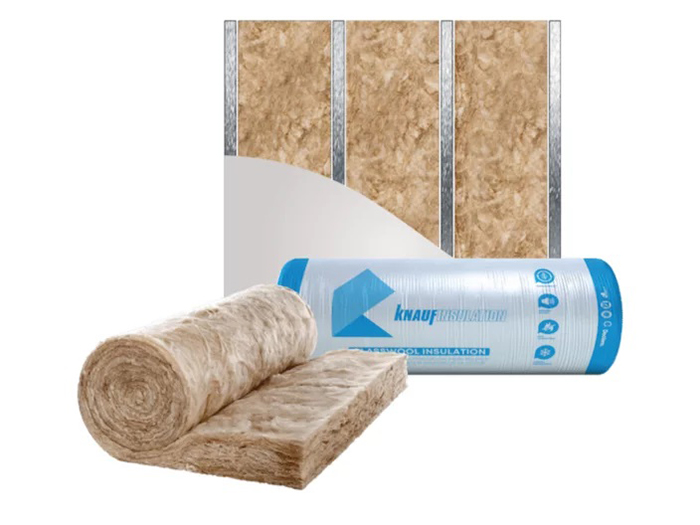
Knauf Insulation Acoustic Partition Rolls
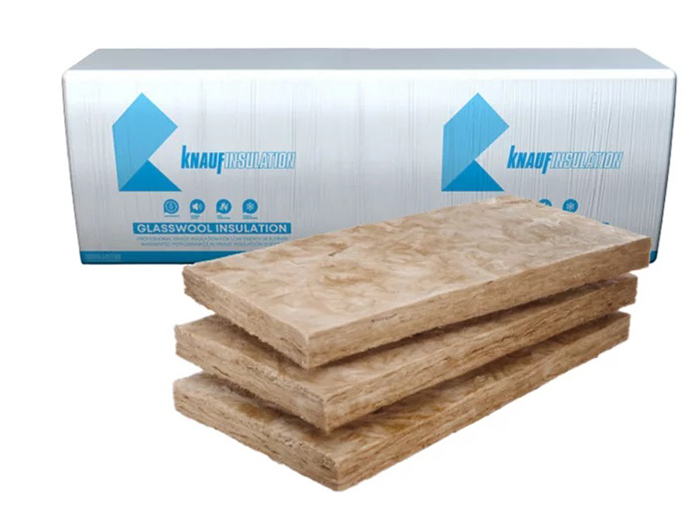
Knauf Insulation Acoustic Batts
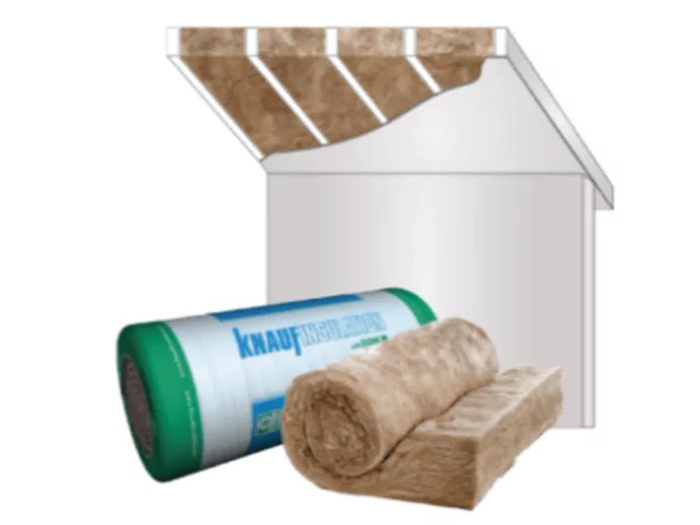
Knauf Insulation Roof Blanket