D&C Built commenced their latest construction project comprising of two towers in Perth’s iconic waterfront, Elizabeth Quay, situated above a shared podium and plaza, with the two buildings having a combined total area of 70,000 square metres.
The tower closest to the river is a 58-storey residential complex comprising of 250 high quality apartments. These apartments will enjoy views across Perth up to Rottnest Island with the tower also incorporating Australia’s only high-rise public art gallery and viewing deck. The adjoining building will feature a hotel and serviced apartments with a total of 190 short stay accommodation units. This tower will also feature contemporary commercial space with retail outlets and wellness centre facilities.
What were the insulation requirements?
Insulation in high-rise buildings is crucial for energy efficiency, occupant comfort, and acoustic performance. Given the scale and scope of the project, it was critical for the insulation to pass stringent testing within the BGC wall systems and provide excellent thermal and acoustic performance along with non-combustible classification. Acoustic insulation was necessary to ensure the residents experience the highest comfort levels with no compromise to privacy and health.
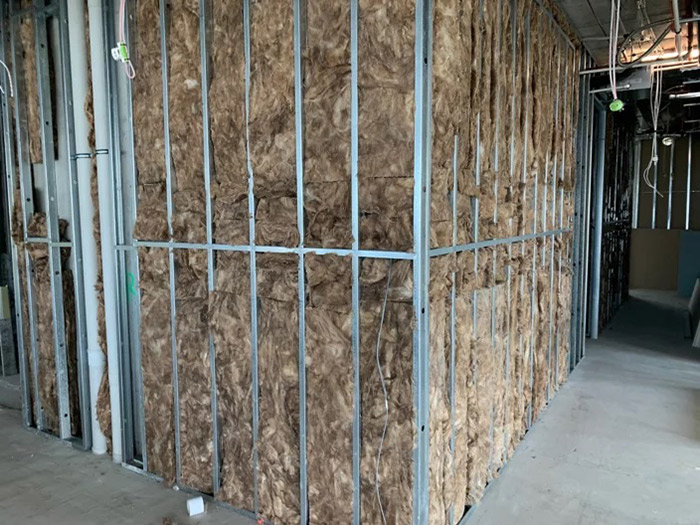
Which Knauf Insulation products were specified for the project?
Knauf Insulation products were involved in rigorous testing within BGC wall systems, achieving a non-combustible classification in strict accordance with AS 1530.1. Knauf Insulation 14kg/m³ acoustic batts were chosen for the walls between the residential and short-term apartments to create an airtight inter-tenancy barrier, which would improve the thermal and acoustic envelope. Knauf Insulation 24kg/m³ acoustic batts were used for GTEK™ Protect Shaftwall, achieving the required Rw50, and complying with the National Construction Code of Australia.
What assistance did Knauf Insulation provide throughout the project?
Knauf Insulation was able to provide independent certification that established confidence in the insulation materials being specified, such as BRANZ and Codemark, which simplified the compliance process. Further certifications such as Declare and Eurofins Gold were able to demonstrate the products’ safety during installation.
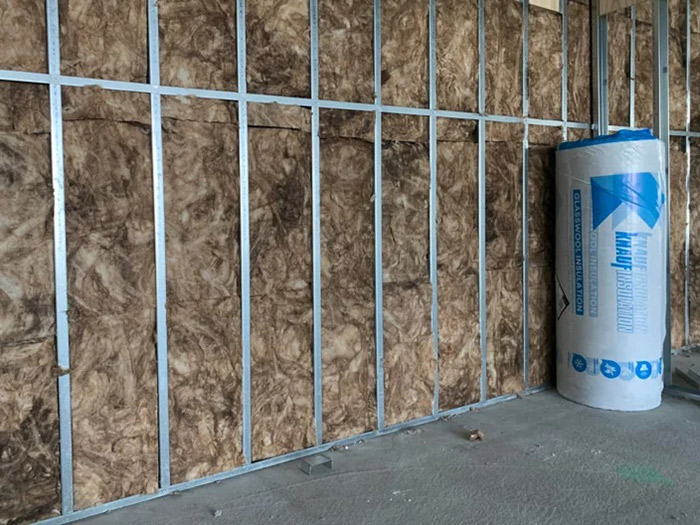
Why was Knauf Insulation the preferred choice over competitor solutions?
Knauf Insulation’s range of glasswool was chosen over foam boards because of its non-combustible status as well as the high thermal and acoustic performance that it delivered in the BGC systems.
Knauf Insulation was chosen over other mineral wool products due to its availability in the region as well as its compression packaging for ease of storage and on-site handling.
What new products or technologies were used to achieve a sustainable building?
Knauf Insulation is the only glasswool in Australia to have Global GreenTag GreenRate Level A Certification, which helped contribute to the 5-star Green Star and 5-star NABERS ratings of both buildings. Knauf Insulation is also the only glasswool in Australia to have Declare certification, classifying the products as ‘Red List Free’. This provides installers and ultimately occupants with the peace of mind that there are no harmful chemicals in the building.
What was unique or special about this project?
- Perth’s largest commercial development in recent years
- The two-tower project is valued at $1.1 billion, with a construction cost of $367 million
- The taller tower will stand 58 storeys while the second will be 21 storeys
- Australia’s only high-rise public art museum and viewing area, with views across Perth to Rottnest Island set to become one of the city’s most important tourist destinations
- High performance acoustic insulation tested in BGC wall systems
- Additional insulation used in bathrooms and around pipes to reduce noise