Maxton Fox is a commercial furniture and joinery manufacturer based in Sydney, and committed to manufacturing in Australia for over 50 years. Their vast capability onsite at their manufacturing facility in Western Sydney means they can deliver against many project requirements.
Maxton Fox works in partnership with their clients, which consist of national and multinational building and construction firms to architects and interior designers.
What are some key sustainability aspects of your business and certified products?
At Maxton Fox, we’ve held Environmental Management Systems (ISO 14001) and Quality Management (ISO 9001) certifications for over 12 years. Four years ago, we invested in solar energy and installed 1,000 solar panels on our factory roof so that, over time, we have less reliance on the grid for energy.
In addition to the above, our processes ensure that we are constantly reviewing our waste management and waste minimisation. For example, when working on projects, we ensure we maximise the materials used to reduce waste. We run a metal recycling process so that scrap metal is not wasted, and we recycle other metals for other components. We also ensure timber scraps are turned into items we use and re-use daily such as trolleys and packing pallets for delivery and installation.
Our GECA certified Tasman Workstation has undergone extensive engineering and sustainability research together with Western Sydney University’s Professor of Engineering. Stability, sustainability and circular economy processes have been adopted throughout the entire process from design to manufacture on this workstation.
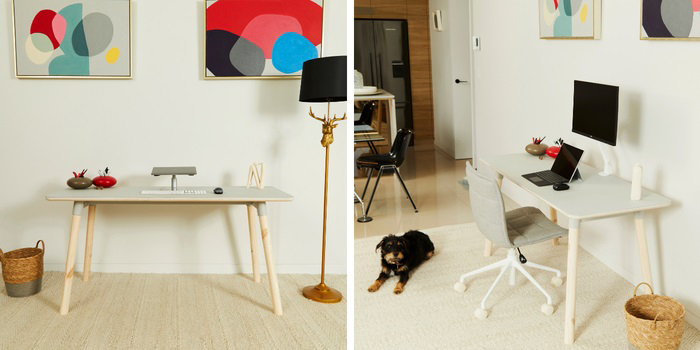
Our Maxton Fox designed and manufactured products are made in-house at our Western Sydney factory facility. Our Maxton Fox workstations are not flat-packed and delivered in boxes. Instead, when delivering and installing our workstations, we protect our items with packing material, which we regularly reuse; so again, we are minimising waste.
Why did you choose to get a GECA certification, and how important is independent certification to you and your customers?
GECA is a globally recognised lifecycle ecolabel. After learning more about the principles and the processes involved in achieving a Level A certification, we couldn’t help but be up for the challenge! Independent certification is extremely important and builds immense credibility.
Did you have to make changes to your product to obtain GECA certification?
Yes, we realised that whilst we were told a particular adhesive was low VOC, we discovered that it was not low enough, and we found the best lowest VOC product on the market. So, this was a valuable learning!
What do you think are the biggest sustainability challenges for your industry right now?
There are a variety of ‘certifications’ required for products to be specified, which becomes costly for manufacturers in Australia to compete with imported products on a price value. Suppliers are bringing cheaper imports into the market and claiming sustainable credentials – how can we validate these claims? Our global industry must embrace credible, robust and third-party verified certification.